As a Senior Sales Consultant at EIKONA Logistics, he knows the requirements of the logistics sector inside out and finds customised solutions.
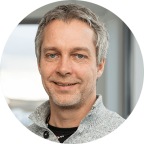
What do appointments at the city office and the loading of a lorry have in common? At best, there is a pre-booked time slot for both! After all, there are few things more annoying than unnecessary waiting – condemned to doing nothing, with all the other things and appointments in the back of your mind that are delayed as a result.
According to recent studies, lorry drivers wait more than 60 minutes on average before they are cleared at the loading bay. This downtime not only costs time and nerves, but ultimately also hard cash, as it means they can complete fewer trips per day. But that doesn’t have to be the case. The magic word: time slot management!
The term time slot management already gives a rough idea of what the topic is all about: the digital control of time slots. If specific windows of time are allocated for delivery, loading and unloading processes, the entire supply chain benefits. On the one hand, shippers and logistics service providers can plan more precisely because they know when which lorry will be dispatched at the loading ramp. Secondly, waiting times are significantly reduced overall, as the available ramps and loading personnel can be optimally planned.
Already knowing in the morning what to expect throughout the day. Being able to control when capacity utilisation at the ramp is at its highest. Meeting deadlines and at the same time being able to integrate spontaneous tours. Do these requirements sound familiar to you as a shipper? Without time slot management, in the best-case scenario, companies manage to get through the day without any major incidents – if they are lucky. However, if some vehicles arrive late or another problem arises, this quickly leads to chaos, traffic jams and peak loads.
A good time slot management tool can help by linking important processes within the supply chain. Whereas in the past, every step often involved a great deal of manual effort, for example announcing the arrival of a driver to the shipper, the software completes many tasks completely automatically. Loading processes are thus perfectly timed and can be controlled digitally. The following paragraphs reveal how this works.
Anyone familiar with the show Domino Day will perhaps remember the feeling of suspense: will all the dominoes fall as planned or will the whole row come to a halt in the middle? The situation is comparable with supply chains: The individual processes are heavily interdependent, and if the lorry loading is delayed, for example, this results in a whole chain of delayed subsequent processes. The solution lies in the digital coordination of time slots. If you can rely on the time slots because they have been realistically planned and can be adjusted, if necessary, this is also good news for all subsequent processes: they can take place as planned.
If you’re thinking: “That sounds complicated!”, don’t worry: It’s not, the digital coordination of appointments is very easy. This is how the process works in an ideal scenario:
APIs and other interfaces enable communication and data exchange with existing systems, such as ERP or telematics solutions. The time slot management software can thus access all relevant data.
Who hasn’t experienced this? You’ve got the date for the parents’ evening at school in mind, but it’s not yet jotted down in the calendar. Now the long-planned dinner with friends is to take place on the same evening – annoying! Double bookings occur especially when not all appointments are planned and recorded in one place. Poor planning can also lead to double bookings or imbalanced capacity utilization in logistics. For example, the ramp personnel may have very little to do between 9 a.m. and 1 p.m. because hardly any lorries need to be loaded or unloaded. In the afternoon, on the other hand, there are traffic jams in front of the yard gate and long waiting times for the individual drivers because not all loading processes can take place at the same time.
However, if the shipper defines suitable time slots from the very beginning to ensure optimum and consistent ramp management, this cannot happen. Transport companies and freight forwarders then select the best time slots for them. This way, they can be sure that the loading process will actually take place in the specified time slot because the ramp personnel are prepared and have scheduled the lorry.
Of course, even the best software cannot prevent a truck from getting stuck in an unplanned traffic jam because there is a route closure on the motorway. However, here’s a scenario the time slot management tool can prevent: The staff at the destination stand at the ramp and wait unnecessarily. If it is communicated transparently that a driver is running late and cannot keep to the booked time slot, it is possible to reschedule as required so that, for example, another lorry is brought forward for loading or unloading. As is so often the case, information is key!
By the way, the driver does not have to provide updates on the ETA (Estimated Time of Arrival) themselves – the system takes care of that. If it is linked to common driver apps and contains a track and trace component, it is always clear where the lorry is currently located, whether it is in a traffic jam and when it is likely to arrive at the shipper.
An “interface between drivers and ramp that acts as a solution to avoid waiting times” – this is what many logistics companies enter into the search engine when they want to optimize their loading processes. A time slot management tool can not only do this, but much more: it significantly simplifies daily planning, enables the digital coordination of bookings, avoids stress peaks, shortens loading times and ensures optimum capacity utilization at the loading ramp. It also handles communication between all parties involved and saves valuable time here, too.
It makes sense: if it is clear in advance how many vehicles need to be dispatched and when, and which ramps are needed for this, the yard and the personnel at the loading ramp can be optimally planned. Of course, sometimes things don’t go according to plan. However, thanks to the status updates, you are informed in good time and can reschedule if necessary. In the end, everyone is happy: customers, shippers and logistics service providers benefit from planning reliability and minimized downtimes with maximum flexibility. Our conclusion: time slot management makes logistics better and faster!
Add a comment