As a design guru, the software developer delves into logistics service providers' requirements like no other. He is passionate about exchanging information securely and efficiently and thus speeding up the physical logistics process.
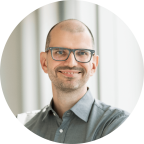
Logistics processes consist of many individual steps and produce a lot of data through regular status scans. What sounds like a good starting position for logistics managers, however, becomes a problem when processes are disrupted: How then do dispatchers quickly find important data and recognise where to take action? Especially if quick action can ensure a successful outcome?
Supply chain event management (SCEM) software provides the support they need. It flags deviations from the target process along the entire logistics chain and thus enables timely counteraction. It scans the flood of information to identify issues that require human intervention. This can only succeed if the following questions are answered when the software is set up:
Companies use SCEM to make their logistics processes more stable, efficient and cost-effective. These systems are needed given the ever-increasing complexity of supply chain management. Connections within the supply chain have become so convoluted that it is almost impossible to monitor supply chains unassisted. Constantly searching all data sources for disruptions is not only time-consuming; it is also economically wasteful. It is far better to apply the principle underlying SCEM systems: management by exception – that is, only intervening when problems occur. Here is an example: If parts for just-in-sequence production are delayed by severe weather or impassable roads, the process managers, production planners and in-house logistics professionals need to know as quickly as possible. That gives them the option of procuring replacements or switching over production. This avoids production downtime and high follow-up costs. If, in addition, rules can be formulated on how to respond to certain deviations, SCEM can also manage the logistics chain independently and modify the process as needed. The data it measures during the process can also be used to generate statistical reports. This data, in turn, reveals trends – and thus reveals weak points in the logistics process.
Supply chain event management can only be transparent if all parties involved in the logistics chain are connected to one another. Only then will all the necessary information, from the initial order to delivery, come together in one central resource: real-time shipment status, estimated time of arrival (ETA), and task management with escalation deadlines. The SCEM software continuously compares these actual values with the predefined target. That frees up supply chain managers to focus on coordination and relaying valuable incident information: Transparency across the entire supply chain is created when the right people receive all the information they need at the right time.
To enable effective supply chain event management, all participants in the logistics chain must be linked with each other. Only then will all the necessary information from order to delivery converge in a central resource: shipment status in real time, estimated time of arrival (ETA) and task management with escalation deadlines. The SCEM software continuously compares these actual values with the predefined target. In this way, it relieves the supply chain manager. With success: he can concentrate on coordination and pass on valuable information on disruptions. Transparency is created across the entire supply chain because the right people are provided with all important information at the right time. In addition, better processes often enable high savings and a significant reduction in transport costs.
Transparency is also the basic prerequisite for efficient multi-company processes. Precise, relevant, and timely information is essential for tightly integrating the entire process chain. Freight forwarders can then pick up shipments faster – and that benefits shippers. Consignees can better plan their downstream activities due to better on-time delivery. The service providers, for their part, reduce their error rate and turnaround times. This allows them to increase the (transport) capacity of their resources. These improvements also reduce logistics costs for everyone involved. Freight forwarders offering this kind of service add value and benefits for their customers in industry and commerce. After all, they are improving more than just their own profit margins.
Add a comment